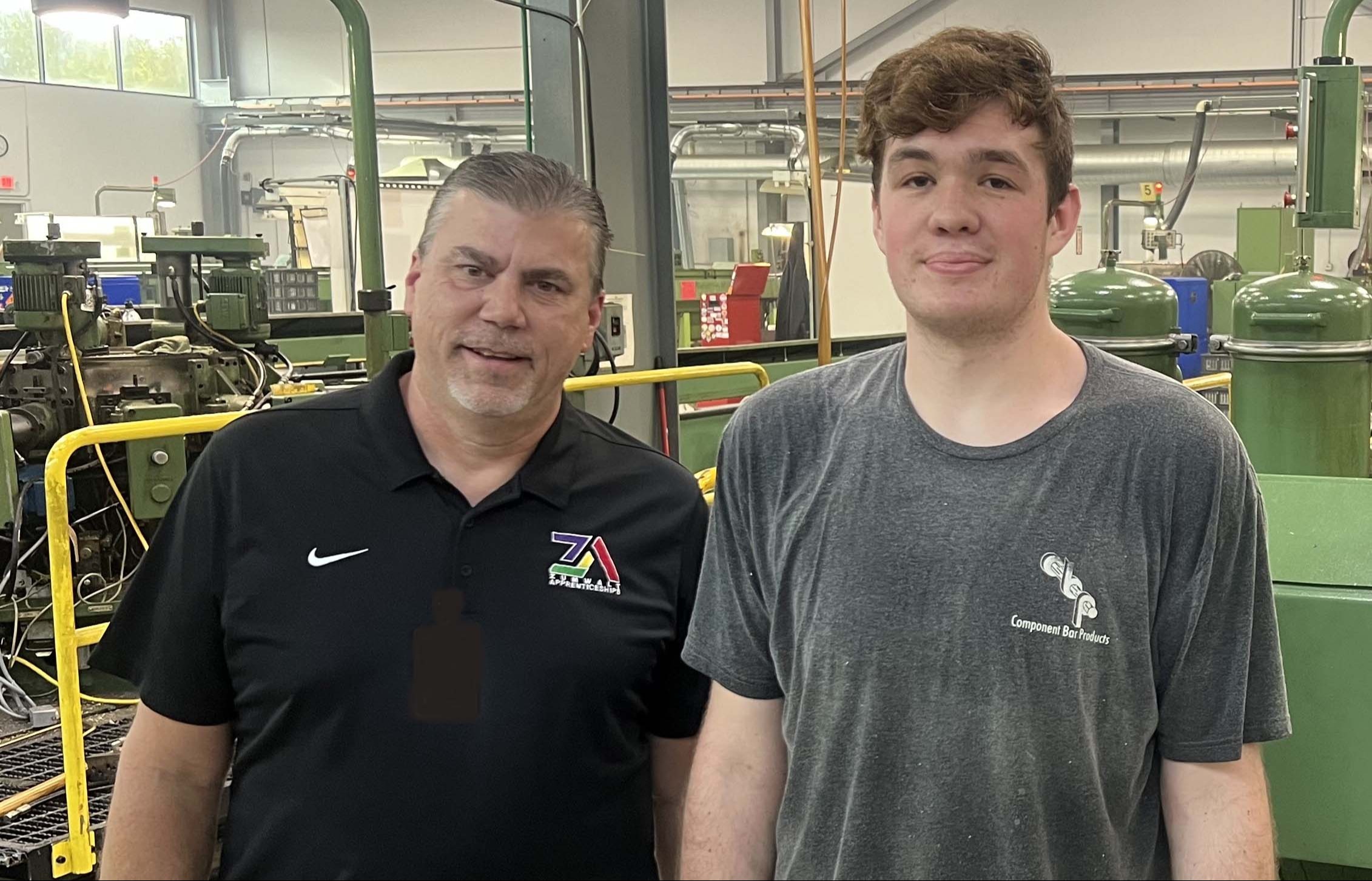
Mason Halbert: A Future Built on Hard Work and Opportunity
Every morning somewhere between 3:30 and 4 AM, Mason Halbert starts his day at Component Bar Products, ready to take on another shift in the high-precision manufacturing industry. At just 18 years old, Mason, a recent graduate of Fort Zumwalt North High School, is already setting himself apart with his dedication and work ethic. What motivates him to wake up before dawn while many of his peers are still sleeping? A career path that matters.
Mason is passionate about his work, and he thrives in an environment where effort is rewarded. "They give back to me as much as I put in," he says about Component Bar Products. This company, a leader in high-volume, high-precision manufacturing, has been operating for 35 years, utilizing Hydromat machines to produce parts for HVAC systems, industrial fittings, and U.S. defense and military ordnance.
From High School Student to Skilled Apprentice
Mason's journey with Component Bar began in 2023 when his high school woods and metals instructors recognized his potential and recommended him for an apprenticeship. Initially, he had concerns about working in a fast-paced, deadline-driven industry, but he quickly discovered that the company allowed him to develop his skills at a manageable pace.
A significant turning point in Mason’s growth was finding a mentor in his lead, Cameron Bach. Cameron not only provided guidance but also took the time to answer questions, offering support that helped Mason gain confidence in his role. "Cameron always had great advice and was willing to help," Mason recalls.
Mason’s plant manager, Jeff Bell, speaks highly of him, stating that his coworkers love working alongside him. "His work ethic and production make him a rock star," Bell says. It’s clear that Mason’s attitude and drive have made him a valuable team member.
A Game-Changing Workforce Strategy
Component Bar Products, like many manufacturing companies, has faced challenges in attracting and retaining skilled workers. John Pollihan, CEO of Component Bar, notes that they have tried numerous strategies—from hosting manufacturing days to providing training facilities—to bring in future employees. However, nothing has been as effective as the apprenticeship program.
“The apprenticeship program has been a game-changer in the outlook of attracting talent and creating a continuous pipeline of workforce for our company,” Pollihan says. By investing in young apprentices like Mason, Component Bar is addressing immediate labor needs and building a skilled and dedicated workforce for the future.
Hard Work Pays Off
Balancing school and work wasn’t easy. While still in high school, Mason worked approximately 25 hours per week. At the time, school wasn’t going particularly well for him—until the apprenticeship program gave him a reason to stay focused. The program required him to maintain his grades and stay on track for graduation. The added structure and motivation led to a significant turnaround in his academic performance.
In November 2024, Mason successfully completed his Machine Operator Apprenticeship. Now working full-time, plus overtime, he's earning a solid paycheck and taking pride in the skills he has developed. Over the past 18 months his confidence and demeanor have grown immensely.
A Future in Manufacturing
When asked where he sees himself in five years, Mason’s answer is clear. He wants to follow in his mentor’s footsteps and become a lead at Component Bar. His ambition doesn’t stop there. Thanks to the 45 hours of college credit he earned through his apprenticeship, Mason is now pursuing an Associate's Degree at St. Charles Community College—an opportunity he might not have considered otherwise.
Mason’s story is a testament to the power of apprenticeship programs in shaping the future of young men and women who are willing to embrace the "learn as you earn" model. Soon two new apprentices will be joining Component Bar, and Mason is eager to welcome them. He hopes to be a mentor, just as Cameron was for him, helping them navigate their first real job and the opportunities that come with it.
Building the Next Generation of Skilled Workers
Currently, the Fort Zumwalt School District has more than 70 students engaged in U.S. Department of Labor apprenticeships across various industries, including advanced manufacturing, healthcare, culinary arts, childcare, paraprofessional education, and information technology. These programs are equipping the next generation with the hands-on experience and technical skills they need to excel in the workforce.
Mason Halbert’s journey is a testament to what’s possible when ambition meets opportunity. His story is one of many that demonstrates how, with the right support, mentorship, and work ethic, young people can build successful careers in high-demand industries—all beginning in high school.